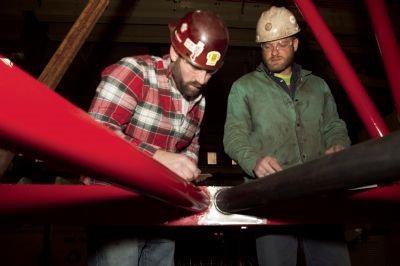
This article is the fifth in ALL’s Day in the Life series, showcasing careers in the heavy lift industry.
Daniel Giera is responsible for four shops at ALL’s main yard in Cleveland: the weld shop, machine shop, paint shop, and trailer shop. But he isn’t a welder, fabricator, or painter.
Trained as a mechanical engineer with a degree from the University of Toledo, Daniel Giera never would have predicted his skills would be put to use at one of the largest crane rental houses on the continent. But like most who work for the ALL Family, his childhood interest in construction equipment partially predicted his future.
“I loved Tonka trucks, climbing on things, riding tractors,” he said. “So even though this isn’t a typical engineering job, it’s actually a great fit.”
A Foot in the Door
Giera joined ALL part-time while he was still in school, training with Raymond “Torch” Pekarski, a memorable figure in ALL’s history. At the time, Giera’s priority was converting Torch’s hand-drawn engineering plans into AutoCAD.
Employees at ALL cross-train to gain experience with different tasks and responsibilities. This helps them understand the bigger picture in a way that wouldn’t be possible if they were focused solely on one task, and it helps managers identify employee strengths.
So when Giera wasn’t converting plans to AutoCAD, Torch kept him busy learning the business.
One of his main responsibilities was doing repair work for equipment that needed maintenance. “When a trailer would come in, I would take all of the appropriate measurements, from every angle. I’d use those to make the new drawings and rebuild it using my engineering background,” he explained. “I worked on a lot of trailers and cabs then.”
The ALL Family used to make all of its own service trucks. Giera would produce the specs, create the material lists, and then help the fabricators interpret the drawings he created. “From a design aspect, I was uniquely qualified to assist [the welders and fabricators],” he said. “It helped them understand why the welds need to be done the way I specified, and it helped me to understand the process to achieve them.”
“I also worked in the shops, doing everything from burning, machining, welding … I even swept floors,” he remembered.
Giera also credits Mike Toth (his immediate predecessor), as well as Torch, for his operational and managerial training. Understanding each of the roles in the weld shop, paint shop, machine shop, and trailer shop now helps him to plan projects and prioritize the tasks for his 20 employees.
Managing Four Shops
Prioritizing for the staff is important because what they do affects just about every piece of equipment in the ALL fleet at some point—and every task starts with an engineered drawing from Giera.
“The ALL Family is as self-service as we can be. We do it all in-house, which cuts out the expense of a third party,” he said. “Our goal is to increase customers’ uptime, help them work more efficiently, and save them money.”
“We also make our own fenders. When a new truck comes in, new fenders need to be designed, and I order the right materials and steel to ensure we can create them,” he said. So when a part comes off the CNC plasma table, a burn table that reduces steel waste, it’s a safe bet that the pieces were originally drawn by Giera.
In Cleveland, Giera has three Manitowoc- certified welders, one of whom is a certified Manitowoc Field Repair welder. “Because we have these guys on staff, we are able to use the manufacturer’s procedures here rather than sending the equipment to Manitowoc for repair,” he explained. “This gives us control of the timing, yet we can still repair to manufacturer specs. That is another way of increasing uptime and saving our customers money.”
That “uptime” is important to Giera, too. He rises early, arriving at the office around 6 a.m., before his crew. “It’s when I get settled in and plan my day,” he said. “I walk through each of the shops to see the progress from the day before, adjust the priorities, and then can have assignments ready for my team.”
Typical engineering work is very theoretical, meaning it’s usually 9 to 5 spent sitting at a computer. But Giera is up and moving all day. Unless he’s working on a design, the early morning might be the only time he’s actually at his desk. “I really enjoy that this is hands-on, and I play an active role in my drawings coming to fruition. Most engineers don’t get that experience.”
Throughout the day, he cycles through each shop, checking progress, inspecting welds, interpreting designs, and providing assistance to members of his crew. “I’m making sure my fabrication guy has the drawings he needs to make the right parts. In another bay, I’ve got repairs going on a trailer,” he narrates. His mind keeps processing the progress. “Does the boom repair guy have the lacing? Are the welders safe and making good welds?” He moves on. “Another guy is making floor anchors, so I make sure he has the drawings for the plasma table, that he has the materials he needs. I confirm the parts are burned correctly and check the welds.” All the while, he is taking calls from branches and coordinating with yards. “And when each piece is complete, there are inspections to be made—by me as well as by third-party inspectors.”
The ALL Family has the largest privately owned fleet of crawler cranes, which means it has its share of track repair. According to Giera, some of that work will now go to West Virginia (see page 24). “Their facility is state-of-the-art, and they’re able to do everything we do here and more. The focus on track repair makes more sense at that location. Previously, we had to ship or haul equipment and tracks to Cleveland for repairs. That took time and cost more.”
The new facilities in West Virginia won’t mean less work for Cleveland. It just means that the company as a whole will work even more efficiently. “I enjoy the challenges of each day. New puzzles. Problem solving. The engineer in me loves a good problem,” Giera said. “I’m task-oriented, and I like to check things off my list. By the time I check one thing off, there’s five new things added. It’s good to be busy.”
Trained as a mechanical engineer with a degree from the University of Toledo, Daniel Giera never would have predicted his skills would be put to use at one of the largest crane rental houses on the continent. But like most who work for the ALL Family, his childhood interest in construction equipment partially predicted his future.
“I loved Tonka trucks, climbing on things, riding tractors,” he said. “So even though this isn’t a typical engineering job, it’s actually a great fit.”
A Foot in the Door
Giera joined ALL part-time while he was still in school, training with Raymond “Torch” Pekarski, a memorable figure in ALL’s history. At the time, Giera’s priority was converting Torch’s hand-drawn engineering plans into AutoCAD.
Employees at ALL cross-train to gain experience with different tasks and responsibilities. This helps them understand the bigger picture in a way that wouldn’t be possible if they were focused solely on one task, and it helps managers identify employee strengths.
So when Giera wasn’t converting plans to AutoCAD, Torch kept him busy learning the business.
One of his main responsibilities was doing repair work for equipment that needed maintenance. “When a trailer would come in, I would take all of the appropriate measurements, from every angle. I’d use those to make the new drawings and rebuild it using my engineering background,” he explained. “I worked on a lot of trailers and cabs then.”
The ALL Family used to make all of its own service trucks. Giera would produce the specs, create the material lists, and then help the fabricators interpret the drawings he created. “From a design aspect, I was uniquely qualified to assist [the welders and fabricators],” he said. “It helped them understand why the welds need to be done the way I specified, and it helped me to understand the process to achieve them.”
“I also worked in the shops, doing everything from burning, machining, welding … I even swept floors,” he remembered.
Giera also credits Mike Toth (his immediate predecessor), as well as Torch, for his operational and managerial training. Understanding each of the roles in the weld shop, paint shop, machine shop, and trailer shop now helps him to plan projects and prioritize the tasks for his 20 employees.
Managing Four Shops
Prioritizing for the staff is important because what they do affects just about every piece of equipment in the ALL fleet at some point—and every task starts with an engineered drawing from Giera.
“The ALL Family is as self-service as we can be. We do it all in-house, which cuts out the expense of a third party,” he said. “Our goal is to increase customers’ uptime, help them work more efficiently, and save them money.”
“We also make our own fenders. When a new truck comes in, new fenders need to be designed, and I order the right materials and steel to ensure we can create them,” he said. So when a part comes off the CNC plasma table, a burn table that reduces steel waste, it’s a safe bet that the pieces were originally drawn by Giera.
In Cleveland, Giera has three Manitowoc- certified welders, one of whom is a certified Manitowoc Field Repair welder. “Because we have these guys on staff, we are able to use the manufacturer’s procedures here rather than sending the equipment to Manitowoc for repair,” he explained. “This gives us control of the timing, yet we can still repair to manufacturer specs. That is another way of increasing uptime and saving our customers money.”
That “uptime” is important to Giera, too. He rises early, arriving at the office around 6 a.m., before his crew. “It’s when I get settled in and plan my day,” he said. “I walk through each of the shops to see the progress from the day before, adjust the priorities, and then can have assignments ready for my team.”
Typical engineering work is very theoretical, meaning it’s usually 9 to 5 spent sitting at a computer. But Giera is up and moving all day. Unless he’s working on a design, the early morning might be the only time he’s actually at his desk. “I really enjoy that this is hands-on, and I play an active role in my drawings coming to fruition. Most engineers don’t get that experience.”
Throughout the day, he cycles through each shop, checking progress, inspecting welds, interpreting designs, and providing assistance to members of his crew. “I’m making sure my fabrication guy has the drawings he needs to make the right parts. In another bay, I’ve got repairs going on a trailer,” he narrates. His mind keeps processing the progress. “Does the boom repair guy have the lacing? Are the welders safe and making good welds?” He moves on. “Another guy is making floor anchors, so I make sure he has the drawings for the plasma table, that he has the materials he needs. I confirm the parts are burned correctly and check the welds.” All the while, he is taking calls from branches and coordinating with yards. “And when each piece is complete, there are inspections to be made—by me as well as by third-party inspectors.”
The ALL Family has the largest privately owned fleet of crawler cranes, which means it has its share of track repair. According to Giera, some of that work will now go to West Virginia (see page 24). “Their facility is state-of-the-art, and they’re able to do everything we do here and more. The focus on track repair makes more sense at that location. Previously, we had to ship or haul equipment and tracks to Cleveland for repairs. That took time and cost more.”
The new facilities in West Virginia won’t mean less work for Cleveland. It just means that the company as a whole will work even more efficiently. “I enjoy the challenges of each day. New puzzles. Problem solving. The engineer in me loves a good problem,” Giera said. “I’m task-oriented, and I like to check things off my list. By the time I check one thing off, there’s five new things added. It’s good to be busy.”
# # #
This article originally appeared in ALL’s Lift Line magazine, Spring 2017.
# # #