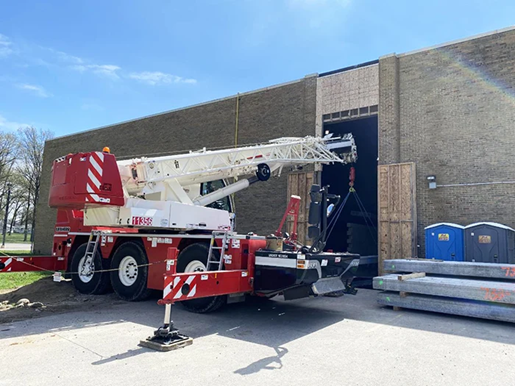
Converting an indoor swimming pool in Lorain, Ohio, into a meeting area and classrooms was going to take precast planks. However, there was no obvious way to get the planks inside the existing, about-to-be-transformed natatorium structure. Not only could a delivery truck not back into the building because there was no doorway large enough, even if it could, the placement of stairwells and other interior elements would have made navigation impossible.
So, what to do? ALL Erection & Crane Rental, a member of the ALL Family of Companies, worked with precast manufacturer Mack Industries on a novel solution for contractor John G. Johnson Construction. ALL started by determining what lift equipment could fit inside the building and Mack reverse-engineered its precast planks to suit the resulting radii and capacities.
Brian Meek, sales rep for ALL Erection & Crane Rental, says they landed on the unique solution of using two pieces of lift equipment – one outside the building, and a carry deck inside – to “hand off” each precast plank.
Set up outside was a Liebherr LTC 1050 all terrain crane. With three axles and a 50-ton capacity, it drives more like a truck crane. Its job was to pick planks off the delivery truck, boom each piece through a doorway, and set it on the floor. Then a 25-ton Broderson IC-400 carry deck crane took over. Here is how Meek explained it: “The Liebherr lays down the precast, the Broderson drives to the doorway, picks up the piece, performs a pick and carry to the set position, then deploys its outriggers before setting the piece.”
It’s a complex series of steps, one that required the Broderson to employ three different load charts for each pick – pick and carry on rubber, intermediate outriggers, and full outriggers.
The capacities and radii necessary limited the size of each plank to 21 feet long and four to five feet wide, and weights of approximately 6,000 pounds. Mack Industries custom-cast each piece especially for the job.
The carry deck crane was, of course, building new interior walls for classrooms while also being confined by the already-existing walls of the natatorium. Eventually, it would be sandwiched between both walls. This limited the reach, and the near radius was limited by the presence of the ceiling, so the plank couldn’t be lifted too closely, either.
Because of a well thought-out plan, ALL worked with Mack Industries to set the 30 precast planks in less than two full days.
“Carry decks aren’t often used on construction projects, but they are ideal for work on flat, concrete surfaces, like industrial plant operations,” said Meek. “Because we were unable to drive the precast directly into the building as we typically do on this kind of project, the Broderson was a perfect solution working in tandem with the Liebherr LTC 1050.”